Une offre complète mât et gréement
Dans VMG Soromap, les initiales signifient Voile Mât et Gréement. Elles illustrent le choix de l'entreprise installée à Rochefort de proposer l'ensemble des produits nécessaires à la construction d'un voilier, chacun nécessitant un savoir-faire donné. Nous nous intéressons ici, avec le responsable de production Nicolas Lecuona, à la fabrication des mâts, espars et gréements. 9 salariés y travaillent au quotidien, pour plus de 300 mâts par an et des centaines kilomètres de câbles de gréement.
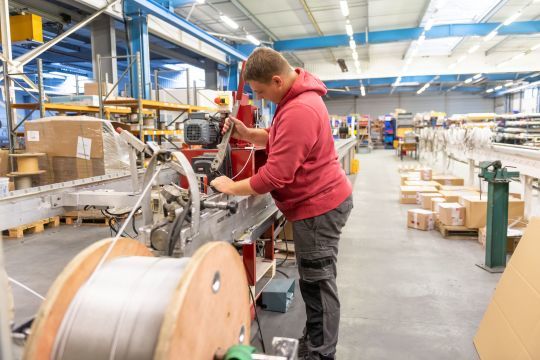
Traçabilité des câbles et accessoires de gréement
Dans le cadre de son activité gréement, l'expertise de VMG Soromap débute dès l'approvisionnement. L'entreprise s'assure de la qualité des câbles achetés auprès de fournisseurs coréens pour l'inox monotoron ou souple destiné au gréement dormant ou d'autres fournisseurs asiatiques pour les filières. L'ensemble des éléments de jonction et embouts sont conçus en interne. Les pièces forgées (embout à œil / à boule) et usinées (embouts simples filetés / ridoirs) sont produits en Tunisie au sein du groupe Soromap, dans une société sœur. "On a une traçabilité sur l'ensemble des matières premières et composants achetés" explique Nicolas Lecuona.
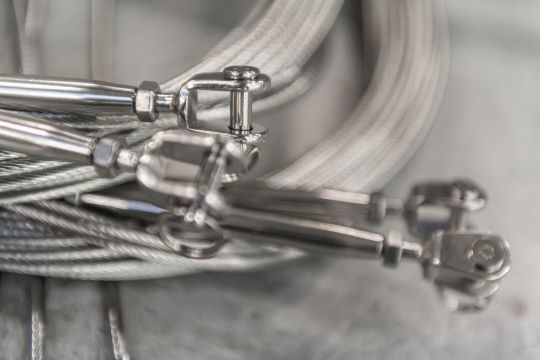
Des gréements sur mesure pour chaque bateau
La réalisation des éléments du gréement se fait soit à partir du gréement existant envoyé par le client en cas de changement identique, soit sur plan à partir du relevé de cadène effectué par un commercial et revérifié par le bureau interne ou des plans du bateau neuf. Les gréeurs professionnels disposent d'un configurateur pour générer automatiquement leurs commandes.
"Ensuite, un ordre de fabrication interne est édité à partir des commandes clients. Il comprend une planche descriptive du gréement avec ses éléments, étai, hauban, galhauban, etc, ainsi qu'une liste des pièces à sortir du magasin et enfin un certificat de conformité" détaille le responsable de production.
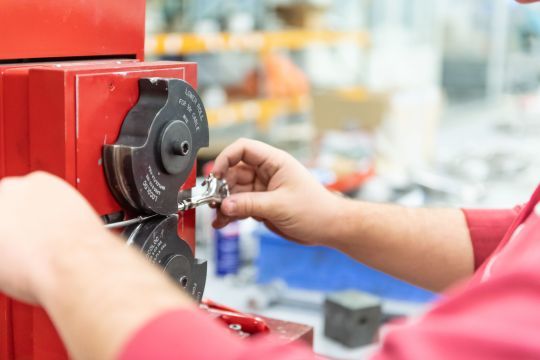
L'opérateur débite les câbles à la bonne longueur, puis les sertit selon la procédure interne. Chaque câble passe ensuite au banc de traction pour valider la qualité de sertissage, en le chargeant jusqu'à 10 à 15 % de la charge de rupture. Il vérifie la longueur du câble. "Le collaborateur signe ensuite le certificat de conformité avant l'envoi au client" souligne Nicolas Lecuona.
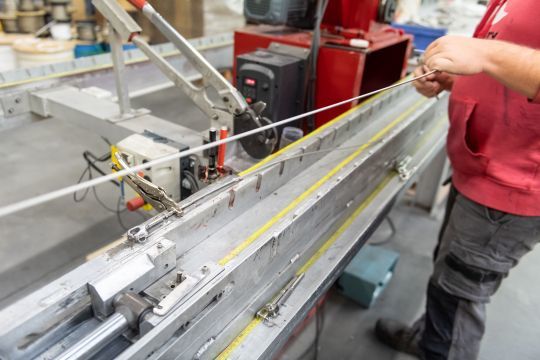
Le produit est ensuite expédié dans le monde entier, avec un conditionnement adapté à la destination, par le département logistique de VMG Soromap.
Des profils de mâts exclusifs
Conçus au sein du bureau d'étude de VMG Soromap, les mâts du fabricant lui sont entièrement exclusifs. Il possède ses propres filières permettant la production en Europe de profilés aluminium extrudés selon ses besoins. "Ils nous arrivent déjà anodisés pour avoir un traitement de qualité industrielle. Nous les stockons ensuite dans une zone dédiée en les manutentionnant avec des sangles pour ne pas les abîmer" explique le responsable.
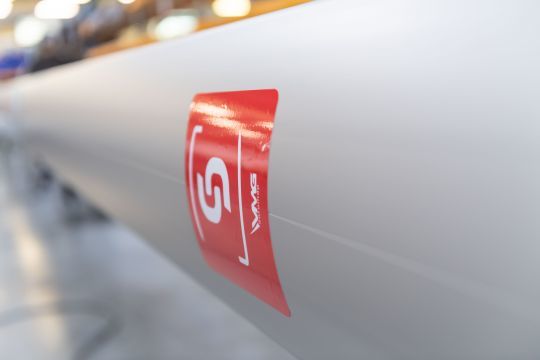
Les produits forgés sont faits dans la filiale tunisienne de Soromap, tandis que les éléments en microfusion inox sont faits en sous-traitance dans des moules propriétés de VMG Soromap.
Usinage et équipement des mâts
La production peut alors commencer, après un contrôle visuel du mât, puis un contrôle géométrique. "On vérifie la rectitude, le vrillage... directement sur le centre d'usinage qui est un marbre précis. Nous avons 2 centres d'usinage : un 4 axes de 18,5 mètres de long et un 5 axes de 23 mètres" précise le spécialiste mât.
Une fois usiné, le mât passe au dégraissage et à l'ébavurage manuel. "Cela permet de vérifier les usinages" indique le responsable.
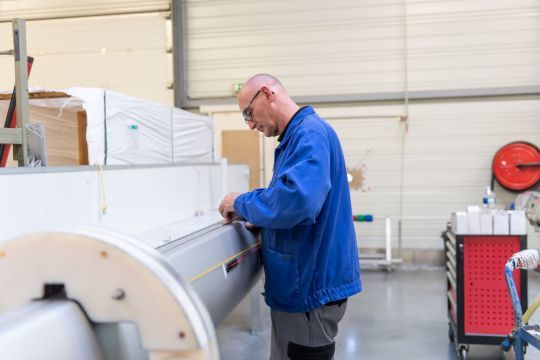
Les opérateurs passent ensuite les tubes iro, gaines de passage des câbles. En parallèle, une personne au magasin prépare l'ensemble des équipements d'accastillage à monter sur le mât. "Le montage sur le mât dure 4 à 12 heures selon la complexité, par exemple s'il y a un manchonnage pour les expéditions à l'export. Ensuite, le chef d'atelier contrôle le mât au décamètre, vérifie que les pièces sont au bon endroit et le matelotage passé là où il faut, qu'il n'y a pas de rayure ou d'anomalie et il signe l'ordre de travail, ainsi que l'opérateur" conclut Nicolas Lecuona.
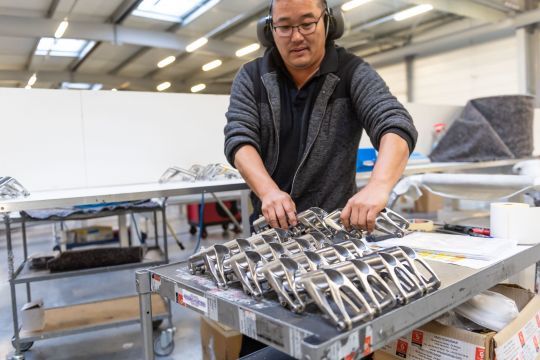
S'adapter au client
Qu'il s'agisse de la finition ou des conditions d'envoi, VMG Soromap s'adapte au client.
Une cabine de peinture de 25 mètres permet d'offrir un laquage ou un coloris de peinture au choix avec l'aide de Soromap SPV, la filiale qui produit et formule ses propres produits. L'atelier de chaudronnerie TIG se charge de réaliser des rétreints en tête de mât pour les plaisanciers en quête de légèreté dans les hauts.
Des tubes annelés protègent les mâts envoyés en grand export.
Grâce à son équipe expérimentée, VMG Soromap répond aux demandes de sa clientèle, concentrée autour de son cœur d'activité, les voiliers de 20 à 60 pieds.